Background technology:
MIM is the abbreviation of metal injection molding, it is a molding method for injection of metal powder its plasticizer mixture into the model. It is the shape needed to mix the selected powder binder before mixing remolding the mixture. The technology is suitable for mass production of small, precise, three-dimensional complex parts with special performance requirements. At present, the product holes in the market are moulded by the front rear moulds in the form of pins. In the process, the small small inserts of the front rear die are forced back, resulting in mold sinking, resulting in poor products.
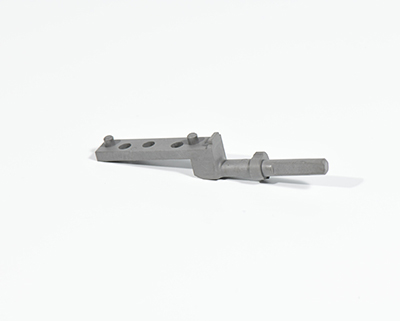
Technology realization elements:
The purpose of the utility model is to provide a kind of MIM mold The bumper inserts increase the pad, reduce the pressure of the inserts, effectively improve the production efficiency, ensure the integrity of the products, make the structure simple reasonable, so as to solve the problems raised in the above background technology.
In order to achieve the above purposes, the utility model provides the following technical proposal: a touch insert of the MIM die, comprising an insert, wherein the insert is connected with a fixed seat, the inserting part is arranged inside the fixing seat, the inserting part comprises a front mold insert a back mold insert, wherein the front mould insert the rear mold insert are clamped, the lower part of the front mold insert the rear mold insert is provided with a mold, a front mold insert a rear part. A clamping needle is arranged at the clamping part of the mold insert, the inserting needle is divided into an upper die insertion pin a lower die inserting needle, wherein the lower die inserting needle is arranged in the mould, the tail end of the lower die inserting needle corresponds to the tail end of the upper die inserting needle, the upper end of the upper die inserting needle the lower die inserting needle are respectively connected with the upper lower two Mian Qiping of the inserts, the upper lower outer surfaces of the inserts are all provided with cushion blocks, which are positioned on the upper die inserting needle. the outer end of the lower die insert.
As a further scheme of the utility model, the inserting needle is provided with eight pairs, each of which is a group, the outer ends of each group are respectively matched with cushion blocks.
As a further scheme of the utility model, the cushion block is a component with strong hardness.