Powder metallurgy, also known as MIM injection molding, is now common in various industries. Some new developing energy such as machinery industry will also be used in powder metallurgy parts. MIM injection into technology, molding sintering is the basic process of MIM injection molding. What is the difficulty of MIM injection molding technology today?
1, other MIM injection molding materials are difficult.
The other MIM is injected into the same material, which can be said as powder, molding sintering. Of course, milling method one hundred, molding method ten, sintering method is also many, the ultimate principle is to adopt the most economical way to meet the requirements of the premise. MIM injection molding technology has the advantages of energy saving, material saving, excellent performance, high precision good stability. It is very suitable for mass production.
2, the traditional MIM injection into iron parts - gear as an example.
A lot of time for mechanical performance requirements are high, in the case of high dimensional requirements, the general density between 6.9-7.1 is acceptable, molding process requirements are high, sintering process requirements are high, prevent sintering deformation, can add Cu sintering shrinkage. With the development of technology, the demand for high performance powder metallurgy iron-based parts is getting higher higher. The density of powder density must be increased. This puts forward higher requirements for forming technology, develops the technology of warm compaction high-speed compaction. The density of components can reach 7.2-7.4.
In order to further improve the mechanical properties of MIM injection molded parts, it is necessary to improve the compactness, which must be considered the powder. The milling technology of powder pretreatment technology has become the focus. The quality of water atomized iron powder plasticized powder processing can reach more than 7.5. This is the level of modern PM parts, which was unthinkable ten years ago.
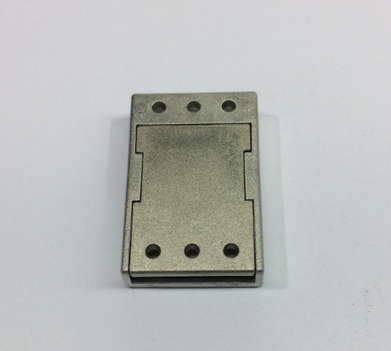